Here's Why Your Favorite Thorne Products Are Sometimes Discontinued or Out of Stock
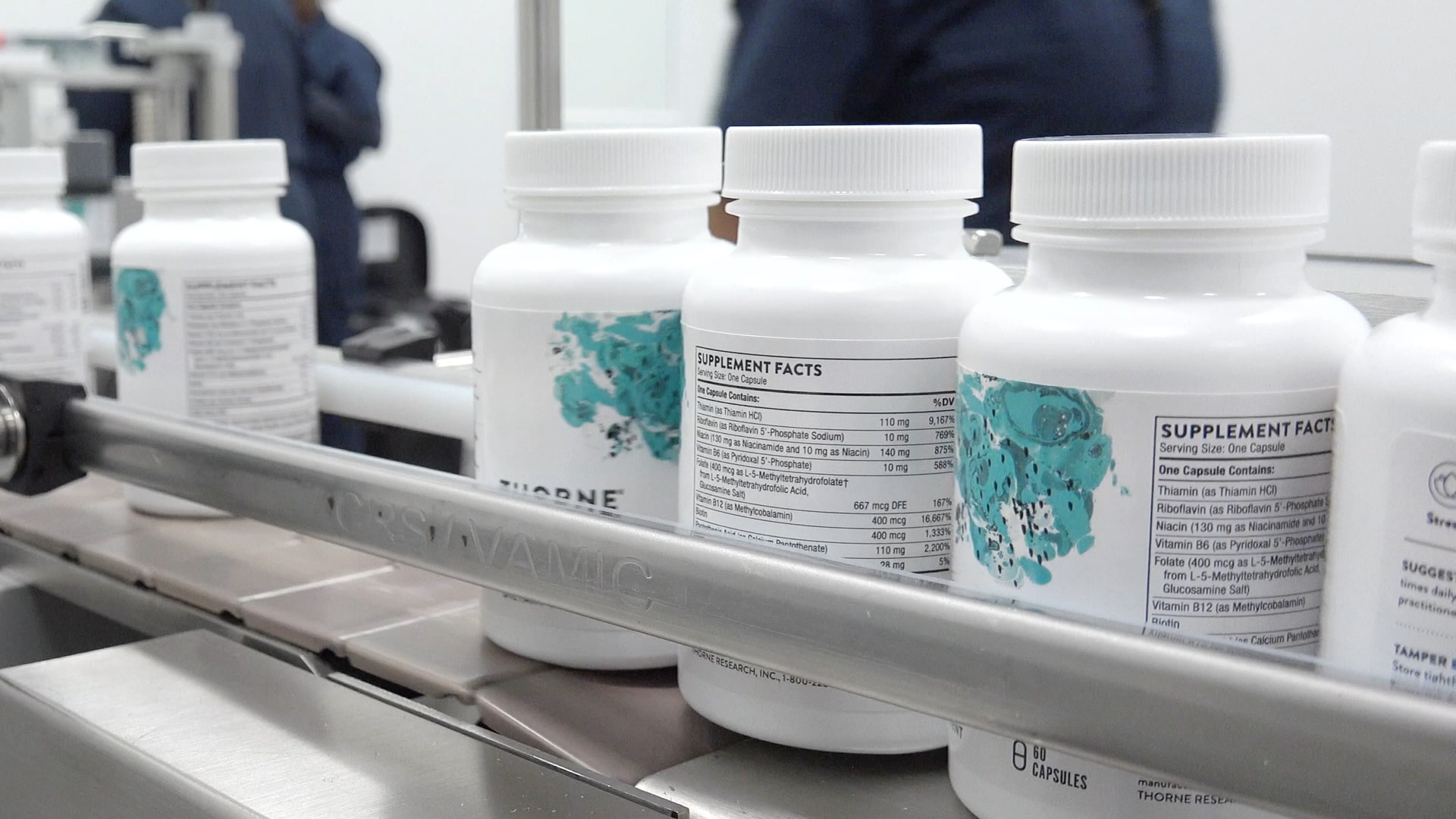
Have you ever tried to reorder a Thorne product only to find it’s out of stock? Or maybe you’re informed it has been discontinued. It can be frustrating. I know because it happened to me once. But there is a reason for it – and it’s one of the reasons why I believe Thorne is the best of the best.
You see, back in 1984, Thorne embarked on a journey to change the supplement industry. The founders believed that when it came to nutritional supplements that “good enough” was not good enough.
For 35 years, Thorne has remained committed to continuously refining each step of the manufacturing process, to perfecting every formula, and to creating carefully considered products made without compromise.
Now this isn’t just some fancy marketing copy, these are words that Thorne lives by. And it’s directly related to why products sometimes go out of stock or are discontinued. Let me explain.
Sourcing exceptional ingredients is time-consuming
In most instances, it takes 16 weeks (sometimes longer) for Thorne to begin and finish the manufacturing of one of its nutritional supplement products. This time period starts when Thorne orders a product’s raw ingredients, and includes the time for testing the raw materials and then manufacturing, bottling, and labeling the product, and finally testing the finished product before it is released for sale.
Thorne could easily speed up this process, except, even though our raw material suppliers conduct their own testing to confirm they meet our specifications and they provide us with a Certificate of Analysis, we take the extra weeks to re-test all of our incoming raw materials to confirm the supplier’s results.
Sometimes we find something a raw material supplier missed – perhaps a contaminant, or perhaps an ingredient doesn’t have the specified potency.
On average, after in-house testing, Thorne rejects about 15% of the raw materials we purchase.
When it comes to your health and wellbeing, you should be absolutely certain that the supplements you take are of the highest quality, which is why Thorne spends so much time on testing. Testing slows things down, no doubt, but Thorne believes product quality – which testing helps to achieve – should be top priority.
Thorne tries to account for raw material rejections, but on occasion, when a raw material fails that has no history of failing, or is replaced by a raw material that also fails testing, then we are left with no alternative but to search for a new, reliable source, which will extend the 16-week manufacturing process and sometimes results in a product being on backorder for an extended period of time.
Crafting and encapsulating high-quality supplements also takes time
It’s not only about finding quality sources of raw materials, Thorne’s actual manufacturing time, even though it’s not the largest chunk of time in the production cycle, is longer than most other supplement companies. Does it have to be? Again, it goes back to our higher standards. Some people could certainly say we make our supplements inefficiently.
And while there are faster ways to make supplements, those manufacturing methods would require manufacturing aids that are on Thorne’s “No List.”
For example, most supplement manufacturers mix magnesium stearate with raw materials during manufacturing. Substances like magnesium stearate are added to speed up manufacturing times, not to improve a product’s efficacy.
Other manufacturers use magnesium stearate or stearic acid because these substances lubricate machinery, helping ingredients to flow into the capsule faster and allowing more material to be packed in a capsule.
Stearates, however, can have a negative impact on the absorption of nutrients, which lowers the supplement’s efficacy.
So Thorne doesn’t use these manufacturing aids. It means Thorne requires more time to encapsulate our products and more time to clean and sanitize our equipment. But it also means that when you take a Thorne supplement, you can trust that it is of the highest quality.
The Thorne manufacturing team typically spends 12 hours cleaning manufacturing equipment, regardless of how long the actual manufacturing time took, which is usually 3-4 hours. Basically, that means Thorne spends much more time cleaning equipment and manufacturing areas than we actually do making our products.
Deciding to discontinue a product
Our science team invests thousands of hours researching, formulating, and fine-tuning Thorne formulas. So deciding to discontinue a product is never an easy decision. When possible, we try to reformulate. This can include removing a problem ingredient if it doesn’t compromise the clinical integrity of the product. Or we might replace the ingredient with another ingredient of the same high quality, clinical efficacy, and consistent supply.
But sometimes reformulation is not an option, and that means discontinuing a product. An example is the discontinuation of Thorne’s Sedaplus – a supplement for sleep support. The problem Thorne had was trying to find a reliable source of valerian root, a key ingredient in Sedaplus, that helped give the supplement its sleep support property.
Lab testing, both in Thorne’s lab and at outside labs, found multiple problems with the valerian root samples we were receiving from various suppliers. If it was not microbial contamination, then it was the environmental pollutant, benzo(a)pyrene – a carcinogenic aromatic hydrocarbon from smoke, vehicle exhaust, and other by-products of incomplete combustion.
The lack of a high-quality valerian root extract meant Sedaplus and its counterpart in our animal health product line, SedaplusVET, were placed on extended backorder. Eventually, when we realized we were not going to find a high-quality valerian root extract, we made the decision to discontinue the product.
Why didn’t we just reformulate? Because we believed the efficacy of Sedaplus truly hinged on the presence of valerian root extract and its synergistic effects with the product’s other ingredients. Someday, if Thorne can find just the right valerian ingredient or the right substitute for valerian, then we might bring Sedaplus back.
Discontinuing a product or an ingredient due to environmental impact
Not being able to find a high-quality ingredient is a key reason for discontinuation. But it’s not the only one. Another reason why Thorne either discontinues a product or reformulates a product is to remove a particular ingredient that has environmental impact and sustainability issues.
Two examples of ingredients we have discontinued for this reason are goldenseal (Hydrastis canadensis) and osha (Ligusticum porteri). While both plant species are particularly useful in immune support formulas, they have both been over-harvested in the wild and are considered endangered species.
So instead, Thorne elected to source other sustainable alternatives to these plants.
We might also discontinue an entire product due to environmental concerns. Several years ago, due to concerns about the krill fishing industry and its potential impact on the wildlife inhabiting the once pristine waters of the Antarctic, we stopped selling Krill Oil.
As an aside, Thorne also considers the environmental impact in our packaging materials. Nearly all of our shipping materials are made of recycled materials. In addition, we use paperless “pick, pack, and ship” – which means we have all but eliminated paper and ink toner from our shipping procedure.
It always comes down to what is best for your health
That’s what I love about Thorne. Even if it results in lost revenue, expending more time, or discontinuing a best-selling product, Thorne will not compromise on quality.
It’s our promise to you that we will never use a raw material or sell a product that we would not use ourselves or recommend to our families and friends. So the next time you see your favorite Thorne product out of stock – or see that it’s been discontinued – it’s because Thorne truly cares about what you put in your body.